- Data integration in manufacturing combines data from various sources into a unified platform, enabling data-driven decisions. Common methods include ETL, ELT, data virtualization, and CDC.
- Data preparation cleanses, transforms, and structures integrated data for analysis. Key steps involve data quality assessment, cleansing, enrichment, and transformation.
- Manufacturing benefits from data integration and preparation through use cases like predictive maintenance, quality control, supply chain optimization, energy management, and production optimization. However, challenges include data quality, volume, security, integration complexity, and governance.
Data is the key
In the manufacturing sector, data is generated from a multitude of sources, including production equipment, sensors, ERP systems, and quality control systems. To harness the full potential of this data, effective data integration and preparation are crucial. These processes are fundamental building blocks for creating an enterprise data platform, a centralized repository that unifies data from disparate sources. Typically, data integration involves consolidating raw data into data lakes, where it undergoes initial preparation before being transferred and refined within data warehouses.
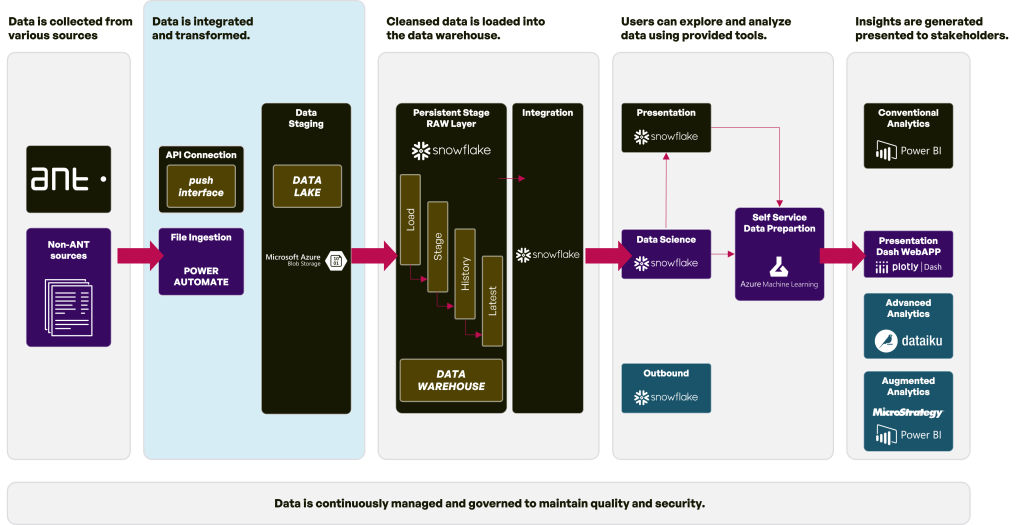
Data Integration in Manufacturing
Data integration in a factory setting involves consolidating data from various sources into a unified platform. This process is essential for creating a comprehensive view of operations and enabling data-driven decision-making.
Common methods of data integration in manufacturing include:
-
- Extract, Transform, Load (ETL): This traditional approach involves extracting data from various sources, transforming it into a standardized format, and loading it into a data warehouse. While effective, it can be time-consuming and resource-intensive.
-
- Extract, Load, Transform (ELT): This method prioritizes speed by loading raw data into a data lake first, followed by transformation as needed. It is suitable for handling large volumes of data but requires robust data processing capabilities.
-
- Data Virtualization: This approach creates a virtual view of data from multiple sources without physically moving it. It offers real-time access but might have performance limitations for complex queries.
-
- Change Data Capture (CDC): This method tracks changes in source systems and applies them incrementally to the target system, improving efficiency and reducing data replication.
Data Preparation in Manufacturing
Once data is integrated, it often requires preparation to ensure its quality and suitability for analysis. This involves cleaning, transforming, and structuring data.
Key data preparation steps in a factory setting include:
-
- Data Quality Assessment: Identifying and addressing issues such as missing values, inconsistencies, and outliers.
-
- Data Cleansing: Correcting errors, standardizing formats, and removing duplicates.
-
- Data Enrichment: Adding contextual information to enhance data value.
-
- Data Transformation: Converting data into a suitable format for analysis, including aggregation, normalization, and deriving new variables.
Challenges and Considerations
Implementing data integration and preparation in a factory setting presents unique challenges, such as:
-
- Data volume and velocity: Manufacturing generates vast amounts of data at high speeds.
-
- Data quality: Ensuring data accuracy and consistency from diverse sources.
-
- Data security: Protecting sensitive manufacturing data.
-
- Real-time requirements: Some manufacturing processes demand immediate data access for decision-making.
By carefully selecting and implementing appropriate methods, manufacturers can overcome these challenges and unlock the full potential of their data.
使用案例
Data integration and preparation in manufacturing can be applied to a wide range of use cases, including:
-
- 预测性维护: By integrating data from sensors, equipment maintenance history, and production schedules, manufacturers can predict equipment failures and schedule maintenance proactively, reducing downtime and increasing productivity.
-
- 质量控制: Combining data from quality control inspections, production parameters, and customer feedback can help identify quality issues early in the process, preventing defects and improving product quality.
-
- Supply Chain Optimization: Integrating data from suppliers, inventory levels, and demand forecasts can optimize inventory management, reduce lead times, and improve supply chain responsiveness.
-
- Energy Management: Analyzing energy consumption data from production equipment can identify energy-saving opportunities and reduce operational costs.
-
- Production Optimization: Integrating data from production lines, machine performance, and product yield can optimize production processes, increase output, and reduce waste.
Challenges
While data integration and preparation offer significant benefits, manufacturers face several challenges:
-
- Data Quality: Ensuring data accuracy, completeness, and consistency from diverse sources is crucial.
-
- Data Volume and Velocity: Manufacturing generates vast amounts of data at high speeds, requiring efficient data handling and processing capabilities.
-
- Data Security: Protecting sensitive manufacturing data from unauthorized access and breaches is essential.
-
- Data Integration Complexity: Combining data from various systems with different formats and structures can be complex and time-consuming.
-
- Data Governance: Establishing data ownership, access controls, and data quality standards is essential for effective data management.
了解更多信息

制造数据分析--利用企业数据平台挖掘洞察力
Manufacturing Data Analytics: Unlocking Insights with an Enterprise Data Platform Manufacturing is undergoing a digital transformation, fueled by the vast amounts of data generated across

数据仓库与数据湖,有哪些区别?
Data Lakes and Data Warehouses: Cornerstones of Modern Manufacturing The manufacturing industry is undergoing a data revolution. With advancements in technology, factories are generating unprecedented

工厂环境中的数据整合与准备方法
Data is the key In the manufacturing sector, data is generated from a multitude of sources, including production equipment, sensors, ERP systems, and quality control