Production optimization and related analytics is important for all businesses, regardless of industry. However, there are companies with special characteristics. This group includes, among others, the pharma cosmetics sector characterized by various forms of cosmetics and a large amount of raw materials used in production. In order to avoid overproduction of waste, highly advanced technologies are used. The example of MES implementation at the cosmetic company shows how profound the benefits of the implementation can be in terms of waste reduction.
ANT implemented solution for a one of the most recognizable Polish cosmetics company. The core of its business is a production of luxurious cosmetics, which is located in the central Poland.
The offer of client’s brand is very diverse. Although these products can be boiled down to one common denominator – they are beauty products. These include creams, gels, application ampules, powders, liquids, scrubs and ointments. As a result, there is a risk of large potential manufacturing waste due to the natural production process, and there is a need to reduce waste.
Optimizing production, eliminating potential sources of errors and issues, and increasing efficiency – these were the company’s primary goals after internal analyses and audits revealed the need to streamline production processes.
The following were indicated as key issues:
- low – relative to potential – OEE indicator
- no measurement of actual cycle times
- too many micro-stops
- too long, and too frequent, 转换
Implementation of changes based on ANT
Based on the gathered data showing the state of production in the factory from an analytical point of view, a pilot ANT system was implemented, initially designed for one production line. The concept was quickly expanded, and today the ANT system covers all eight production lines in the factory. The basic step that was the foundation of any changes leading to 生产优化 was the refinement of the system for communicating with the machines. The changes in the first stage covered the transmission of signals from machines – within PLCs or I/O module – in order to gather all data about production process, such as production execution, waste, states, speed.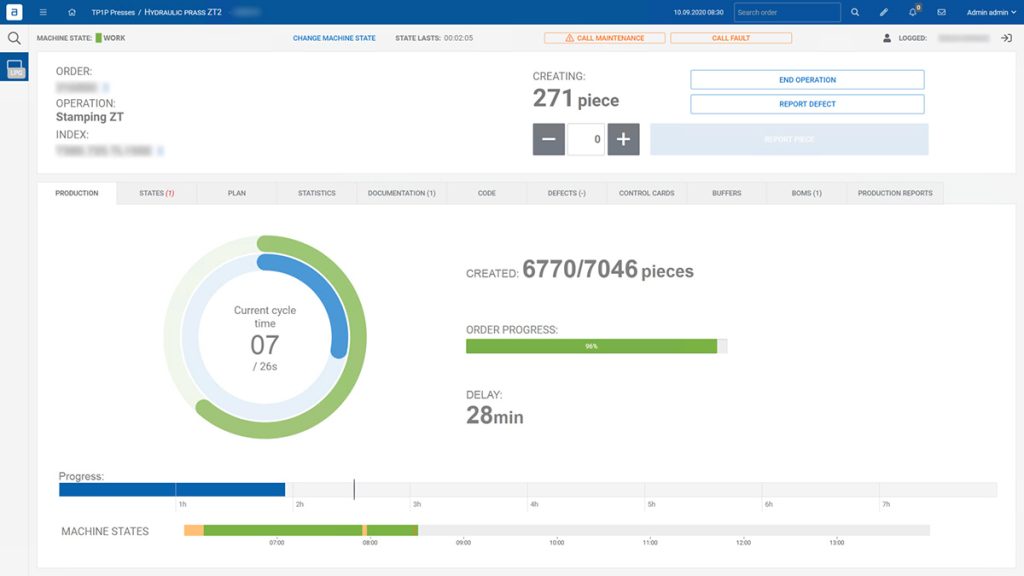
- tube maker (IMA)
- filler (MLB)
- sealer (Unilogo)
- cellophane wrapper (Sollas)
- packing machine (Logopak)
- labelling machine (Unilogo, PAGO)

Results of implementing an MES in the cosmetics factory
Automation in data collection and production monitoring has become the cornerstone of innovation. This includes gathering date from PLC, sensors, and input data collected by operators
This allowed better control of the following elements and processes:
- production counters
- real manufacturing waste volumes
- condition of machines
- causes of individual breakdowns
An important change in the operation of the factory was the flow of data in case of irregularities and deviations from the set standards. Automation has resulted in decisions being made on the basis of notifications sent – importantly – in real time and not by taking into account a delay. This was yet another step towards production monitoring and optimization. Through the MES, also the individual statuses and progress of the production steps were analyzed in real time.
How to reduce production waste, and how important is early notification of failures and their causes in practice in the factory? The example of production lines in the company shows significantly faster reaction and presence of technical service in case of problems detected by the system.
However, the effects of change can be viewed in a much broader way. In addition to the already mentioned faster reaction of the maintenance and technical department, the awareness of the importance of the processes taking place in the factory has also increased. Thanks to the step-by-step display of operations, the operator has a more flexible approach to 交接 and production processes.
This factor also proved to be of importance in terms of identifying and analyzing the causes of micro-stops and manufacturing waste. Although on an individual scale they are not perceived as a threat, collectively they can pose a major problem in terms of a company’s production efficiency. The elimination of minor downtimes has resulted in more seamless execution of production orders.
Also important – when concerning MES factory’s – was the automatic calculation and display of KPIs in real-time.
Company performance after implementing the MES
When analyzing the results of MES implementation in the cosmetics factory, the following can be noted:- more available production time,
- increased OEE,
- decreased number of micro-stops,
- reduced changeover time.
本条中的产品

MES 系统 - 制造执行系统 - ANT 解决方案
System MES – Manufacturing Execution System 0 % operating time increase 0 % defects quantity reduction 0 % material consumption reduction 0 % changeovers time