在实施MES之后,我们通常会注意到一个奇怪的效果。在大多数情况下,在系统上线后,OEE系数比安装前低。通常情况下,变化会导致一开始就把事情变得更糟。不幸的是,这种下降不仅是由工作方法的改变造成的,而且还有其他原因。
你相信你的生产报告吗?
我们经常遇到以下情况。一个操作员在下班时完成一份纸质生产报告。从理论上讲,他应该定期这样做,但(正确地说!)生产更重要。他注意到他生产了多少零件,发生了多少导致返工和报废的缺陷。这是最容易的部分。当他需要将目标与当前状态进行比较时,麻烦就开始了。所以:他应该生产250个单位,但他生产了190个。60个单位所需的时间发生了什么?快速计算一下:那是两个小时......15分钟开始生产,15分钟完成一个班次,计划30分钟的换班时间被延长了30分钟。这就剩下了半个小时,这属于所有接受的类别,称为 "微停"。吁。完成了。
问题是:那么我们是否应该将生产报告的质量归咎于经营者?绝对不是!他没有有效和快速报告生产的工具,这不是他的错。做一个简单的练习,并尝试在工作日结束时逐分钟进行重建。你在8小时内都做了些什么?不看你的日历或待办事项清单就做吗?
操作员的主要任务是在正确的时间内生产质量好的物品。所有其他活动都应该被简化、自动化和最小化。根据不确定的生产数据做出决定,就像依靠运气。我们可能会击中根本原因,但这是改善OEE的最佳方式吗?
实施MES是创造新标准的一种方式
在理论上,OEE的计算似乎很简单:性能x质量x可用性。我们看到了对这些系数的最不同的解释。实施MES是一个很好的机会,修改KPI和系数,说明生产健康。我们将消除这样的问题:集团中的几家工厂对OEE的计算方式有些不同,但结果是根据一个指标进行比较的。
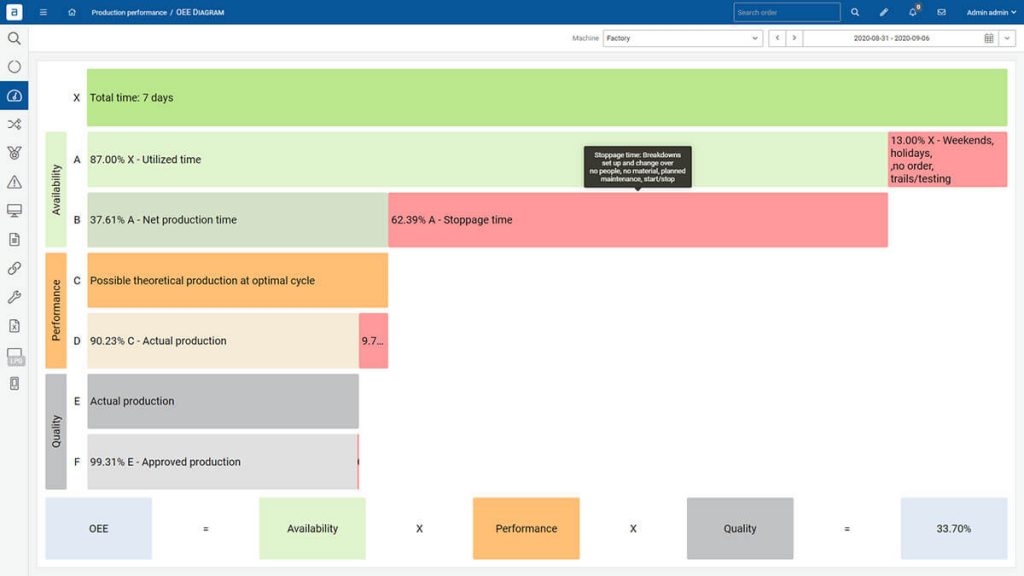
那么是否有一个单一的、通用的方法来计算每个行业和工厂的OEE?不幸的是,不是...系数本身的定义是不同的,取决于生产类型。例如,在自动化生产中,微停可以是任何短于30秒的停顿,半自动化 - 5分钟。
这里应该有一个经验丰富的合作伙伴,它将帮助标准化的KPI。在ANT公司,我们为不同行业做了600多个实施项目。在MES实施过程中,我们的任务是为您的工厂在最佳实践计算方面提供建议。值得为整个集团提出这样一个标准,以便将结果作为 "苹果对苹果 "进行比较。
自动化的数据采集将彻底改变你的生产报告
可用性是指我们用于生产的时间与计划生产的时间。实施MES的最大好处之一是数据采集的自动化。所有的状态都是根据工厂的字典和代码定制的。然后,机器可以自动发送关于停机的通知,或者以最简单的方式,系统存储一个生产和非生产时间。在第二种情况下,操作员可能被要求把停工的原因。是否这样做不会影响OEE,但它将允许更准确地识别可用性下降的根本原因。
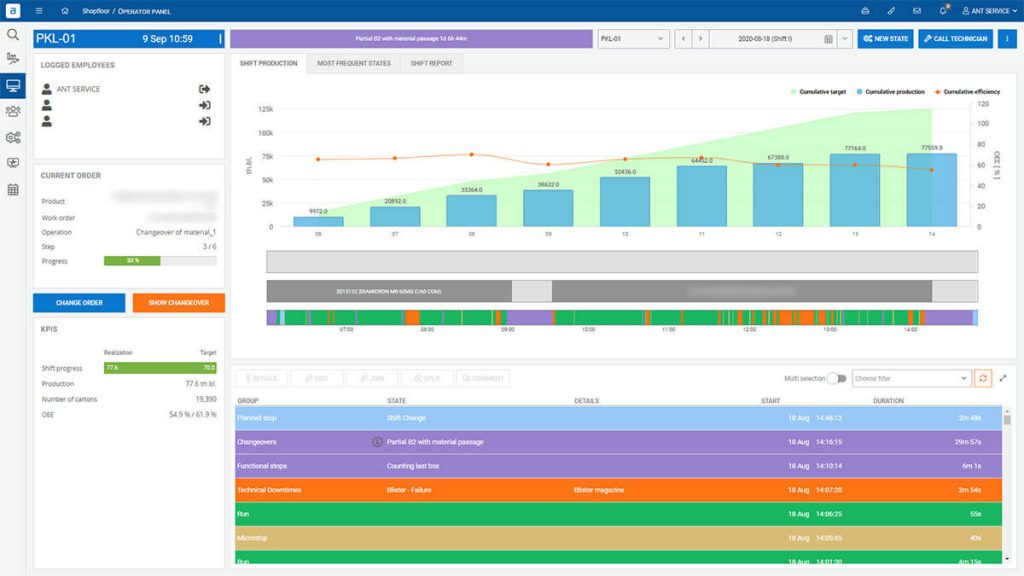
另一件事是对排定的生产时间的解释。它可以采用各种形式,例如,在转换方面。下面是3种最流行的方法:
- 我们将所有的转换时间视为机器可用性和OEE的减少。毕竟,我们可以利用这些设置时间进行生产。
- 我们把计划中的更换时间视为不包括在生产计划的时间内。让我们假设,更换时间为40分钟,而不是计划的30分钟。在这种解释下,只有10分钟会影响OEE的下降。
- 我们将整个更换过程视为从计划生产时间中排除的时间。更换工作不会减少OEE。
ANT智能工厂允许你自动计算你的可用性与机器连接。我们的工程师将创建一个关于从您的机器收集数据的概念,无论您使用的是全新的还是传统的设备。
更好地了解缺陷、返工和废品情况
计算质量的任务表面上看起来很琐碎。毕竟,质量是符合质量标准的项目数量与所有制造项目的数量。但是我们应该如何处理返工?
我将描述两种最常见的方式,如何将返工纳入OEE:
- 我们将返工所需的时间视为未安排的时间。那么返工对OEE没有影响,但会减少TEEP。在生产后分批进行返工的情况下,这个方案似乎最为合理。当零件第一次进入生产过程时,通过降低质量系数来减少OEE。
- 我们将返工视为新的原材料,返回到技术规定的操作中。这种方法影响了OEE。所有的系数将被第二次计算。在当前生产订单期间进行维修的情况下,这种选择似乎是最合理的。在这种情况下,你应该密切关注返工的零件,以避免出现相同项目维修次数过多的情况。你可以考虑在2-3次返工后将项目报废。
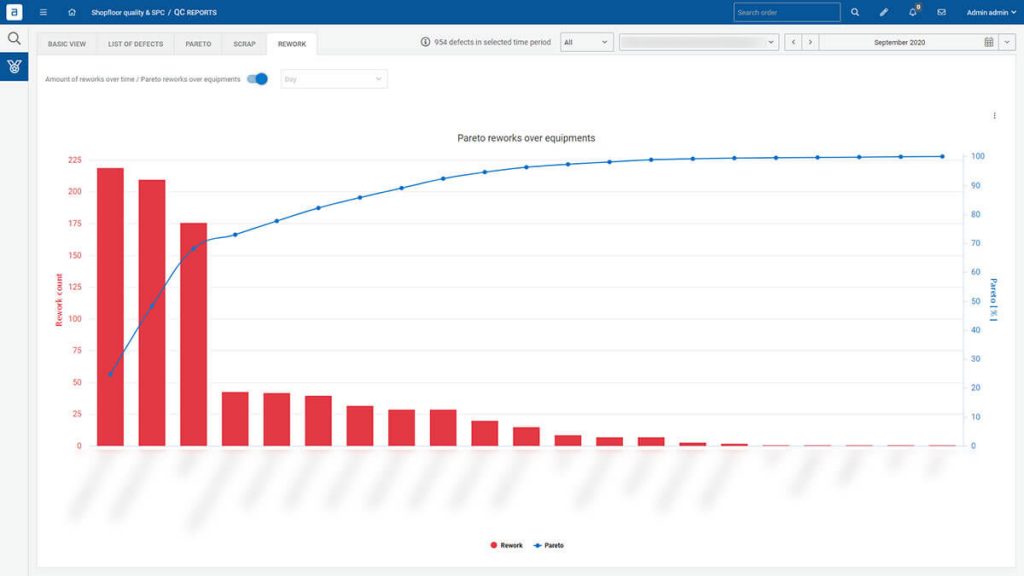
一个有趣的方法是有可能把产生缺陷的机器来源的责任。发现缺陷的操作并不总是它的来源。得益于ANT智能工厂系统,你可以重新计算工厂的OEE,在发现后期生产步骤的缺陷之后。
正确的周期时间是获得真正性能价值的一个关键
性能是实际循环时间与理想循环时间的比值。微停对性能有很大影响。然而,许多工厂将 "标准生产速度 "作为理想时间。这是造成OEE值被夸大的一个原因。
为了充分了解你的OEE并寻求改进,你应该使用最大的理论生产过程速度作为理想周期时间。任何其他方法都会隐藏真实的性能,并通过隐藏损失来提高OEE。
操作人员无法记下每一个微停的原因。机器可以通过与PLC的深度通信自动报告其原因。当一条生产线由许多机器组成时,找到生产线停止的真正原因并不是简单的手动操作。微停算法是由ANT公司开发的,它可以自动地并且精确。它是一种算法,可以通过适当的警报,负责识别造成生产线停工的机器。操作员可以完全集中精力于生产,因为整个报告过程是自动进行的。
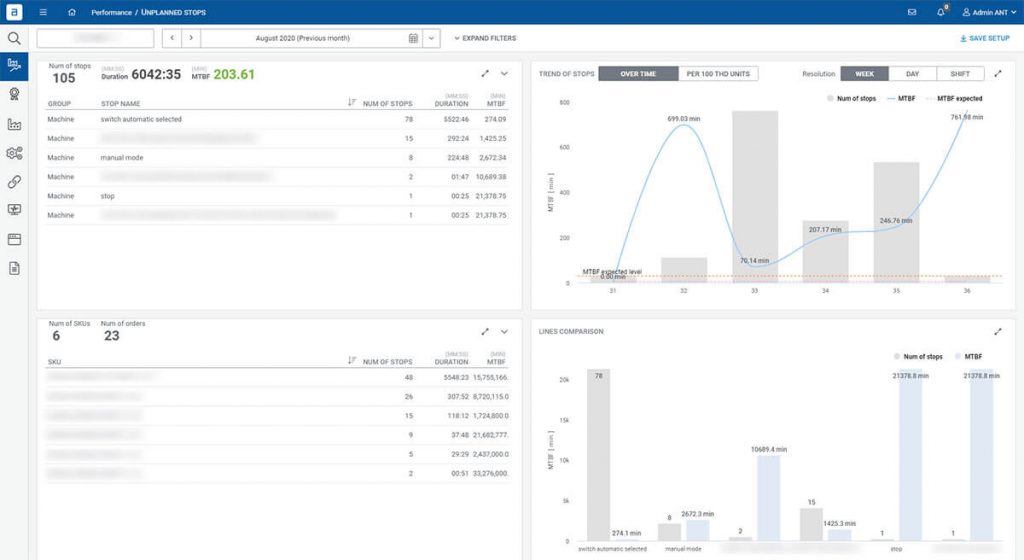
生活中的例子
工厂经理穿过车间,看到机器不工作。操作员们正在熙熙攘攘地整理机器。到了周末,生产报告已经准备好了。OEE在80%水平,并且没有生产停顿,特别是缺乏 "清理机器 "的状态。工厂经理不相信这个生产数据和OEE值。在实施ANT MES后,OEE将下降到60-65%.最后,改善流程和提高产量的真实数据将被提供。ANT工程师将开发计算OEE的最佳方法。在这个工厂的机器状态中,计划内和非计划内的停机时间将不再是不明确的。修订后的OEE系数将显示出需要立即改进的领域。
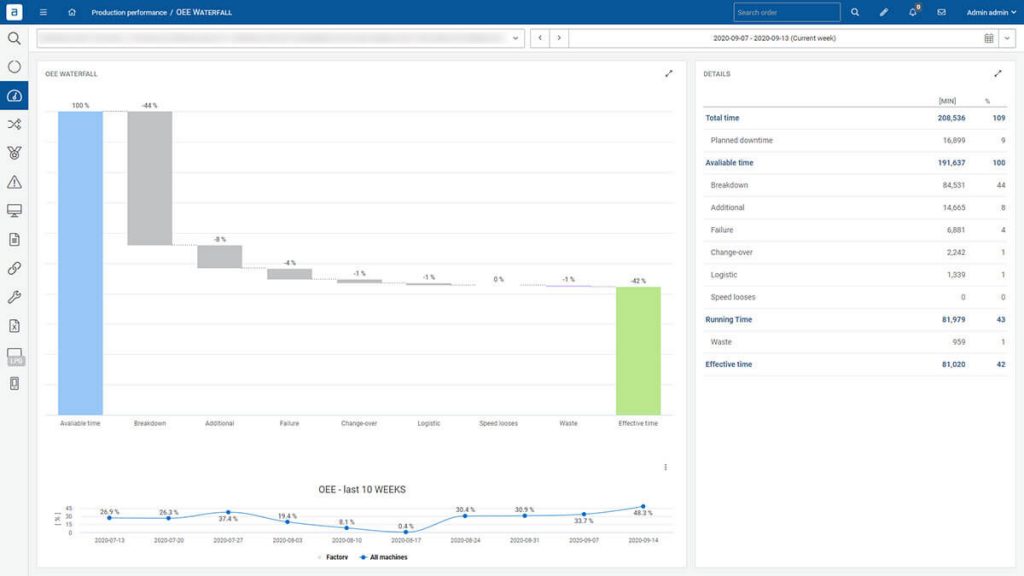
第二种情况是一个4个工厂的经理,他知道集团没有一个计算OEE的标准。每个工厂都以自己的方式进行计算,因为 "流程不同"。事实并非如此,OEE是一个可以对集团进行标准化的指标,能够显示机器的真实效率。经理将得到ANT智能工厂平台,它允许比较工厂首先确定需要改进、培训或LEAN行动的领域。
摘要:
上面讨论的例子并没有涵盖定义可用性、性能和质量的所有挑战。这只是表明问题的复杂性。简单地说,在实施MES后,有3个主要原因导致OEE值下降:
- 修订和统一OEE的计算方式。与MES供应商讨论被认为是理所当然的定义,并根据行业的趋势和最佳实践进行更新。
- 改变报告方式,从手动到自动。与PLC的集成,自动化信号的复制,或安装适当的传感器,实时发送机器状态的数据。周期时间、微停或生产进度被自动计算。
- 更详细的报告。每个生产的项目都将被报告,连同每个缺陷、机器状态或返工。由于没有猜测的空间,报告的质量将是毋庸置疑的。
你更喜欢哪种选择?生活在对生产问题的盲目中,还是真实的数据?联系我们,免费咨询如何将OEE的计算方法适用于您的生产。

克里斯托夫-比亚韦克
高级制造系统工程师
本条中的产品

MES 系统 - 制造执行系统 - ANT 解决方案
System MES – Manufacturing Execution System 0 % operating time increase 0 % defects quantity reduction 0 % material consumption reduction 0 % changeovers time