- Overall Equipment Effectiveness (OEE) is low due to one or more of the following factors: availability, performance, and quality.
- Availability may be low due to unplanned downtime, downtime duration, and lack of improvement in KPIs. Unplanned downtime can be caused by reactive maintenance, failing to gather information about downtime, slow reaction times by maintenance services, and lack of updated information.
- Unplanned downtime: This can be caused by equipment failures, power outages, and other disruptions. Unplanned downtime is a major contributor to low OEE because it reduces the amount of time that the equipment is available to produce good products.
The OEE is the result of three factors, these being availability, performance, and quality. It’s no secret that improving just one of the factors immediately increases the value of the OEE and therefore brings about benefits for the business in its entirety. In the manufacturing sector achieving optimum results across all three areas is key to operating a successful line since they all individually contribute to the viability of the product or service and the profitability.
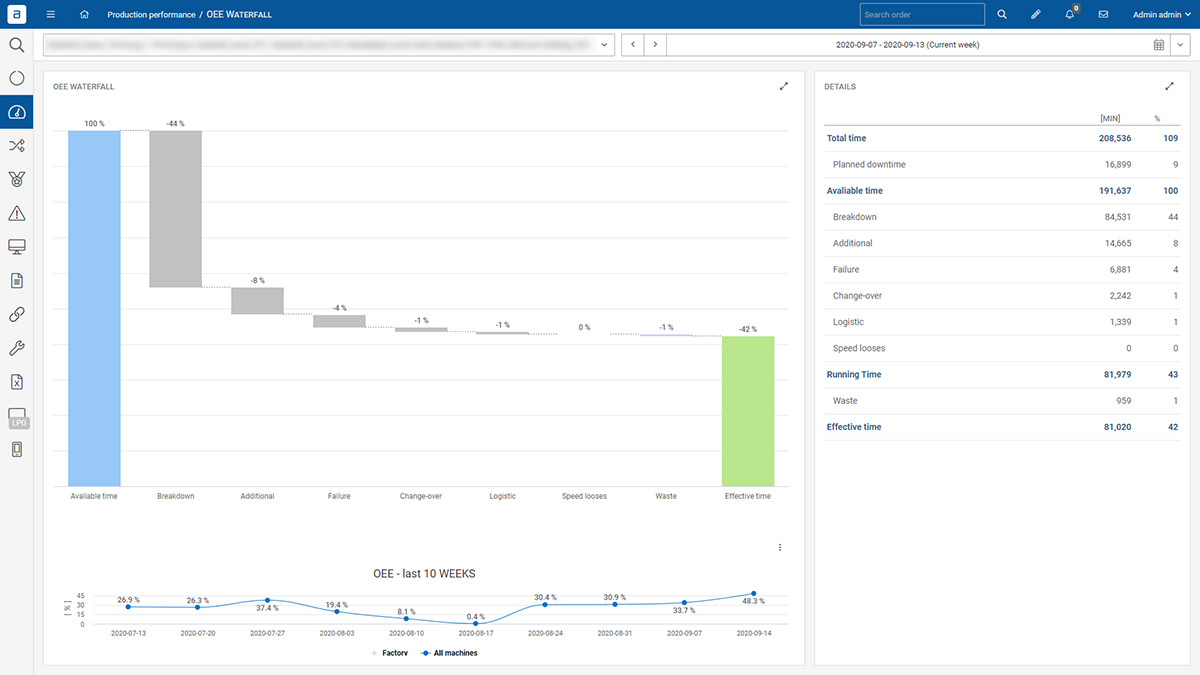
可用性 - 让你的时间真正发挥作用
This factor essentially encompasses any events that have the potential to bring any planned production to a halt for a sustained time. Though downtime is a necessity in the manufacturing industry, it should be kept to a minimum to minimize losses and ensure maximum productivity. There are three main ways that this can impact the overall OEE.
1.太多的非计划性停机时间
This is often due to reactive maintenance. However, failing to gather information about the real reasons for downtime can also prevent improvements from being made in this regard.
2. Downtime that drags on for a sustained period
维修服务部门的反应速度慢,手动调用维修,未能收集机器运行历史,或缺乏最新信息,都是主要原因。
3.没有对关键绩效指标进行衡量和改进
MTTR (mean time to recovery), MTBF (mean time between failure), and MTTF (mean time to failure) all have a part to play in both measuring and improving key performance indicators.
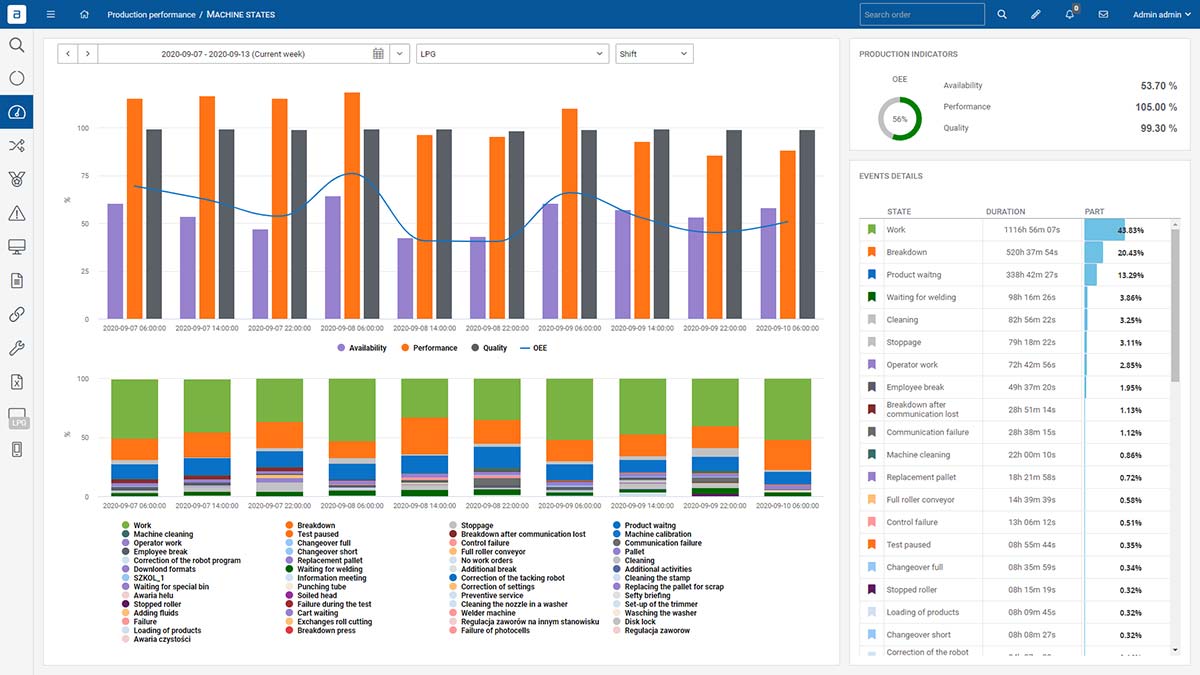
ANT’s endorsed approach to availability is the Andon maintenance module. The Andon maintenance module seeks to reduce such issues by compiling the history of repair reports and using the most recent failures as hints, measuring maintenance reaction times, providing relevant maintenance services along with the causes of downtime, and taking KPI measurements (MMTR, MTBF, MTTF) regularly.
性能 - 发现道路上任何潜在颠簸的能力
The performance takes into account anything that causes the manufacturing process to run at less than the maximum possible speed when it is running (including both Slow Cycles and Small Stops).
However, it’s important to highlight that this particular factor is not associated with units produced, but rather with the equipment or technology used to run the manufacturing line itself. Here, adjustments can be made to boost the efficiency and capability of the line in question.
4.慢速循环
这通常与缺乏对实际周期时间的监测、未能实现自动化、缺乏任务调度或在特定时间范围内有太多的微观停顿有关。
5.长时间的生产启动
Multiple changeovers are among the most common culprits in these cases, although manual communication with laboratories or quality control departments can also impact production launches.
6.缺乏操作员培训
这可能是由于缺乏对操作人员的分步数字指示,入职时间过长,或者在生产和生产目标方面缺乏透明度。
To combat these three reasons for limited performance, ANT has created Digital Documentation and Paperless modules. These enable you and your manufacturing team to display digital information to the operators, categorize documentation such as changeovers and quality controls, guide operators through production and changeovers using step-by-step activities, and automate communication with the laboratory.
It is hoped that this tool will enable you to make your line more efficient and, as a result, boost your overall productivity. Although it may seem cliché, it’s often true that the key is in the finer details, and although a micro stop may seem insignificant, a micro stop module is designed to open your eyes to their potential impact.
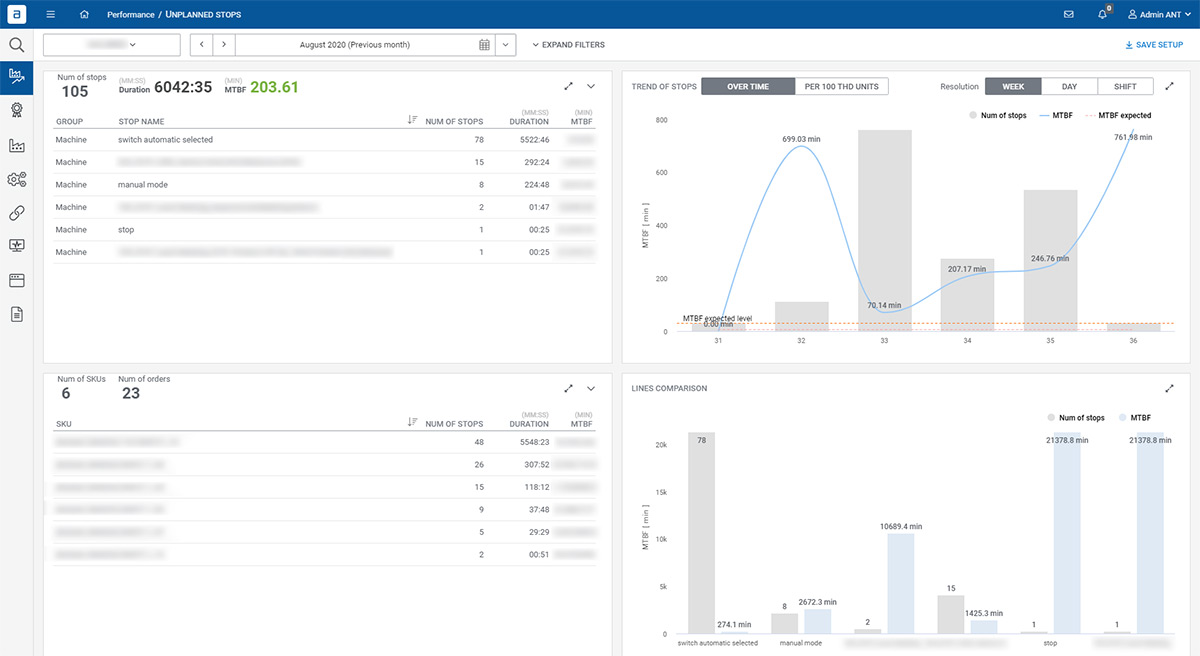
质量--对细枝末节的近距离检查
另一方面,质量考虑到了不符合质量标准的制造部件,包括需要返工的部件。换句话说,它是衡量生产线工艺产量的一种手段,以及缺陷或修改对它的影响。
7.缺陷太多
A lack of analysis in defect production stands out as the most common cause, although cyclic activity lists for operators can also influence the number of defects detected.
8.在开始生产前没有对所用材料/工具/工艺参数进行验证
Cross-checks with used materials batches in the ERP system used material codes in BOM lists are essential in this case, however, it is also crucial to ensure that the machine setpoints (recipes) are correct (manually by the Operator or automatically by ANT system & PLC)
9.L对不稳定过程的认识
This is commonly associated with a Lack of SPC diagrams & control charts & condition-based monitoring. That said, failure to implement automatic counting of how many cycles the tool has made (tool life cycle monitoring and regeneration plan) can also influence late recognition.
ANT seeks to remedy these issues through the launch of its Quality Inspections module, which helps operators and other line management staff to make more informed decisions, by providing them with automated feedback and detailed instructions. The module is also capable of producing a series of quality reports covering specific aspects such as defects.
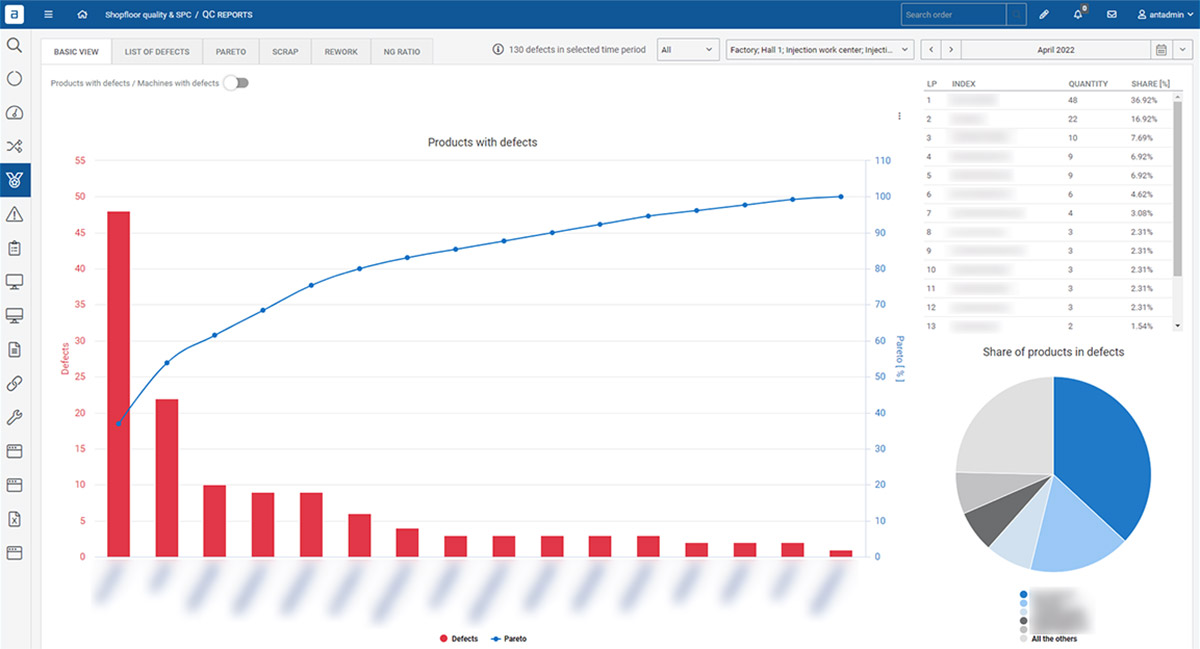
影响OEE的一般原因
10.OEE方程
It’s worth bearing in mind that the use of manual calculation methods is often inefficient, many companies also tackle the OEE calculation rather unobjectively or simply fail to implement it altogether
11. No tools and no plan for what to improve
A lack of tools to compare shifts, operators, machines, lines, and items, no clear method that determines how the gathered data should be used, or a lack of trend analysis also leads to issues in terms of production efficiency.
12.不可靠的数据
这是另一个生产效率的敌人,往往是由于坚持使用纸质文件、信息传达的延迟和机器实时数据收集造成的。
Of course, not all the reasons for low OEE can be attributed to these three main factors. However, our real-time notifications can help to minimize the impact of any issues that you may experience. Our system is also customizable so you can calculate your OEE in a way that works for your business, as opposed to using a standard, one-size-fits-all program.
The real value of OEE can’t be underestimated in manufacturing processes and improving quality, availability, and performance is essential, as difficult as it may seem. The way forward is to make decisions based on numbers instead of personal opinions.
如果你在测量和改善企业的OEE方面需要进一步的帮助,那么不要犹豫,请联系ANT公司的团队,以获得专业的帮助和建议。我们很乐意讨论哪些模块最适合你的具体需求和要求。
Key Takeaways:
- Master the three pillars of OEE: Minimize downtime, optimize production speed, and minimize defects.
- Embrace data-driven decision-making: Leverage automated data collection and analysis to gain valuable insights and continuously improve OEE.
- Move beyond manual calculations: Utilize automated methods for accurate and efficient OEE calculation.
- Achieve superior operational performance: By implementing these strategies, manufacturers can significantly enhance OEE and gain a competitive edge.
本条中的产品

MES 系统 - 制造执行系统 - ANT 解决方案
System MES – Manufacturing Execution System 0 % operating time increase 0 % defects quantity reduction 0 % material consumption reduction 0 % changeovers time