At the forefront of the fourth industrial revolution, smart manufacturing stands as a pinnacle of progress, representing the highest point of tech advancements in the making of goods. This new way of manufacturing is a sharp turn from traditional manufacturing processes that typically require a lot of hands-on work and don’t change very much. Smart manufacturing brings into play the smart use of data, connections between equipment, and high-level computer tech to completely change how we design, make, and send out products.
In this article, we’ll go through the ins and outs of smart manufacturing. We’ll compare it to the old manufacturing processes and show how it could dramatically shift the way things are made in the industry.
Traditional manufacturing processes often involve a set series of steps that don’t change much from day to day. Think of mass production lines that have been around since the early 1900s – they are efficient for making lots of the same thing, but they’re not very flexible.
On the other hand, smart manufacturing processes are like having a super smart assistant that can adapt quickly. One of the coolest parts of smart manufacturing is something called a digital twin. This is a virtual model of the product or production system that can be used to test and improve the manufacturing process without having to change the real thing. It’s like having a practice run in the digital world before you make the real product, which can save a lot of time and money.
With smart manufacturing, factories can make things faster, with fewer errors, and can even switch what they are making more easily to respond to what people want. It’s a big step up from the traditional ways of making things and could lead to a lot of improvements in how we produce everything from cars to phones.
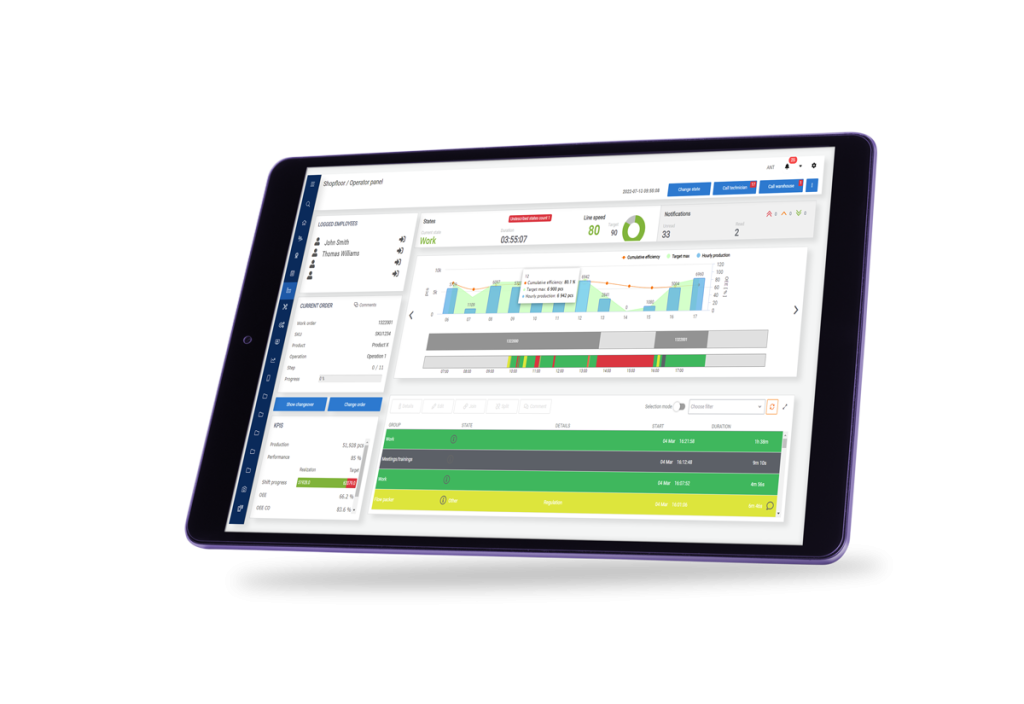
What is Smart Manufacturing?
At its core, smart manufacturing is the symbiosis of advanced machinery and analytics that fosters an interconnected and intelligent production environment. It’s a significant pillar of Industry 4.0, integrating the Industrial Internet of Things (IIoT) to create networks of devices that communicate and collaborate seamlessly.
Some of the key technologies used in smart manufacturing include:
-
- Sensors: Sensors are used to collect data on all aspects of the manufacturing process, from the performance of machines to the quality of products.
-
- Big data analytics: Big data analytics is used to analyse the large amounts of data collected by sensors to identify patterns and trends that can be used to improve the manufacturing process.
-
- Artificial intelligence (AI) and machine learning (ML): AI and ML are used to develop intelligent systems that can make decisions and take actions based on the data collected by sensors.
Understanding Smart Manufacturing
Smart manufacturing is the orchestration of manufacturing processes by advanced technologies that imbue systems with greater flexibility, efficiency, and analytical power. It is a critical element of the fourth industrial revolution, which integrates the industrial internet, big data analytics, and artificial intelligence to create interconnected systems capable of optimisation. The transformation from the first industrial revolution, with its steam-powered engines, through the third that introduced computerised automation, has now culminated in a manufacturing paradigm that is profoundly data-driven and interconnected.
Technologies in Smart Manufacturing
At the heart of smart manufacturing lie several key technologies. Artificial intelligence and machine learning refine the production processes by making them adaptive. Big data analysis turns vast streams of sensor data into actionable insights. The digital twin concept allows for a virtual representation of the manufacturing process, aiding in troubleshooting and optimisation without physical intervention. Technologies like edge computing and cloud computing provide the necessary computational power and data storage capabilities, while the industrial internet of things ensures seamless connectivity among devices.
-
- Artificial Intelligence (AI) and Machine Learning (ML)
-
- AI and ML are powerful tools that can be used to refine and optimize manufacturing processes in a variety of ways. For example, AI can be used to develop predictive maintenance models that can identify potential machine failures before they occur, preventing costly downtime. ML can be used to analyze sensor data to identify patterns and trends that can be used to improve quality control or reduce process waste.
-
- Big Data Analytics
-
- Smart manufacturing generates vast amounts of data from sensors, machines, and other sources. Big data analytics can be used to extract meaningful insights from this data to improve decision-making and optimize operations. For example, big data analytics can be used to identify bottlenecks in the production process, optimize inventory levels, or forecast demand.
-
- Digital Twin
-
- A digital twin is a virtual representation of a physical asset or system. Digital twins can be used to simulate and test manufacturing processes before they are implemented in the real world. This can help to identify and resolve potential problems early on, saving time and money. Digital twins can also be used to monitor and optimize real-time manufacturing processes.
-
- Edge Computing and Cloud Computing
-
- Edge computing and cloud computing provide the computational power and data storage capabilities needed to support smart manufacturing. Edge computing brings computing resources closer to the devices where data is generated, which can reduce latency and improve performance. Cloud computing provides access to scalable computing resources and storage that can be used to process and analyze large amounts of data.
-
- Industrial Internet of Things (IIoT)
-
- The IIoT is a network of interconnected devices that collect and share data. Smart manufacturing relies on the IIoT to connect machines, sensors, and other devices to enable real-time monitoring and control of manufacturing processes.
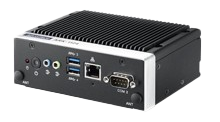
From Traditional to Smart: The Transformation of Manufacturing Processes
The transition from traditional manufacturing to smart manufacturing is marked by a shift from labor-intensive processes to technology-driven solutions. Where traditional methods might struggle with the rigidity and inefficiencies of mass production, smart manufacturing introduces agility and customization. It supplements the enduring practices of the manufacturing sector with precision, digital control, and adaptability, enabling manufacturers to meet contemporary demands for customization and rapid prototyping with unprecedented speed and efficiency.
Traditional manufacturing processes are often labor-intensive and inflexible. Smart manufacturing, on the other hand, is driven by technology and is characterised by agility and customisation.
Some of the key ways in which smart manufacturing transforms traditional manufacturing processes include:
-
- Increased automation: Smart manufacturing technologies, such as robotics and machine vision, can automate many tasks that are currently performed manually. This can free up workers to focus on more complex tasks and improve productivity.
-
- Real-time monitoring and control: Smart manufacturing technologies can be used to monitor and control manufacturing processes in real time. This allows manufacturers to identify and address problems quickly, preventing downtime and quality issues.
-
- Data-driven decision-making: Smart manufacturing technologies generate vast amounts of data that can be used to improve decision-making at all levels of the organisation. For example, manufacturers can use data to optimize production schedules, reduce inventory levels, and improve product quality.
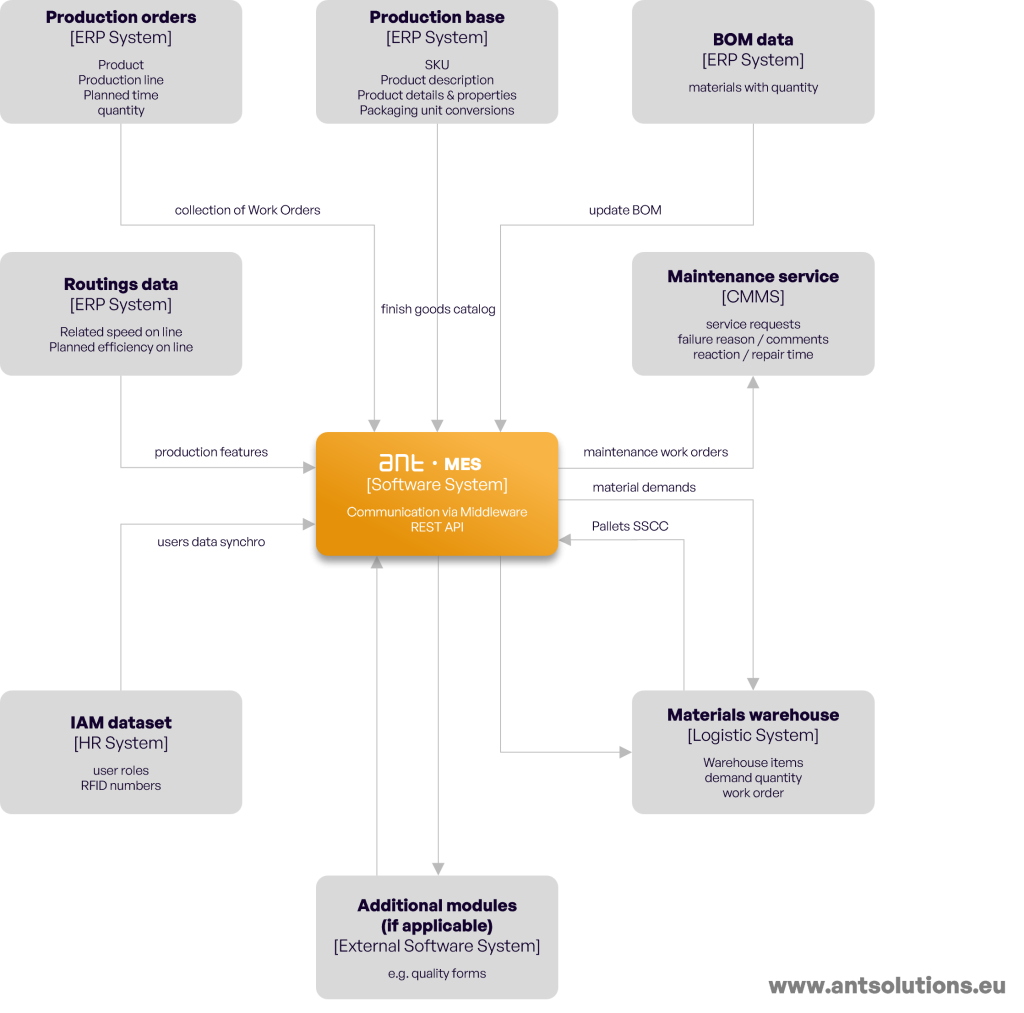
Smart Manufacturing in Action
The concept of smart factories exemplifies the practical application of smart manufacturing initiatives. These factories employ a suite of smart manufacturing software and technologies to monitor and adjust manufacturing processes in real time. The integration of sensor data and AI-based systems, such as computer vision for quality control, has made manufacturing processes easier and more efficient. Robotics systems gather and analyse data to optimize machine performance and production outcomes.
Smart manufacturing is already being used by manufacturers of all sizes to improve their operations. Here are a few examples:
-
- Predictive maintenance: A manufacturer of aircraft engines uses AI to develop predictive maintenance models that can identify potential engine failures before they occur. This allows the manufacturer to schedule maintenance in advance and avoid costly downtime.
-
- Kontrola jakości: A manufacturer of electronics uses machine vision to inspect products for defects. This has helped the manufacturer to improve product quality and reduce waste.
-
- Production optimisation: A manufacturer of food and beverage products uses big data analytics to optimize its production schedules. This has helped the manufacturer to reduce costs and improve customer service.
The Benefits of Adopting Smart Manufacturing Technologies
The adoption of smart manufacturing technologies offers a multitude of benefits. These technologies streamline production processes, reduce operational costs, and enhance product quality. They afford a more robust supply chain and improve after-sales services by providing detailed data analysis. Moreover, smart manufacturing plays a pivotal role in sustainability by minimising material waste and preemptively addressing equipment failures through predictive maintenance.
The Benefits of Smart Manufacturing
Smart manufacturing opens a vista of advantages:
-
- Increased Efficiency and Productivity: Automation and process optimization mean more output using fewer inputs.
-
- Improved Quality: By detecting issues promptly, the manufacturing process is refined, enhancing the end product’s quality.
-
- Obniżone koszty: It paves the way for lower waste production, decreased energy use, and streamlined maintenance.
-
- Increased Agility and Resilience: It equips companies with the flexibility to adapt production processes rapidly to meet market shifts.
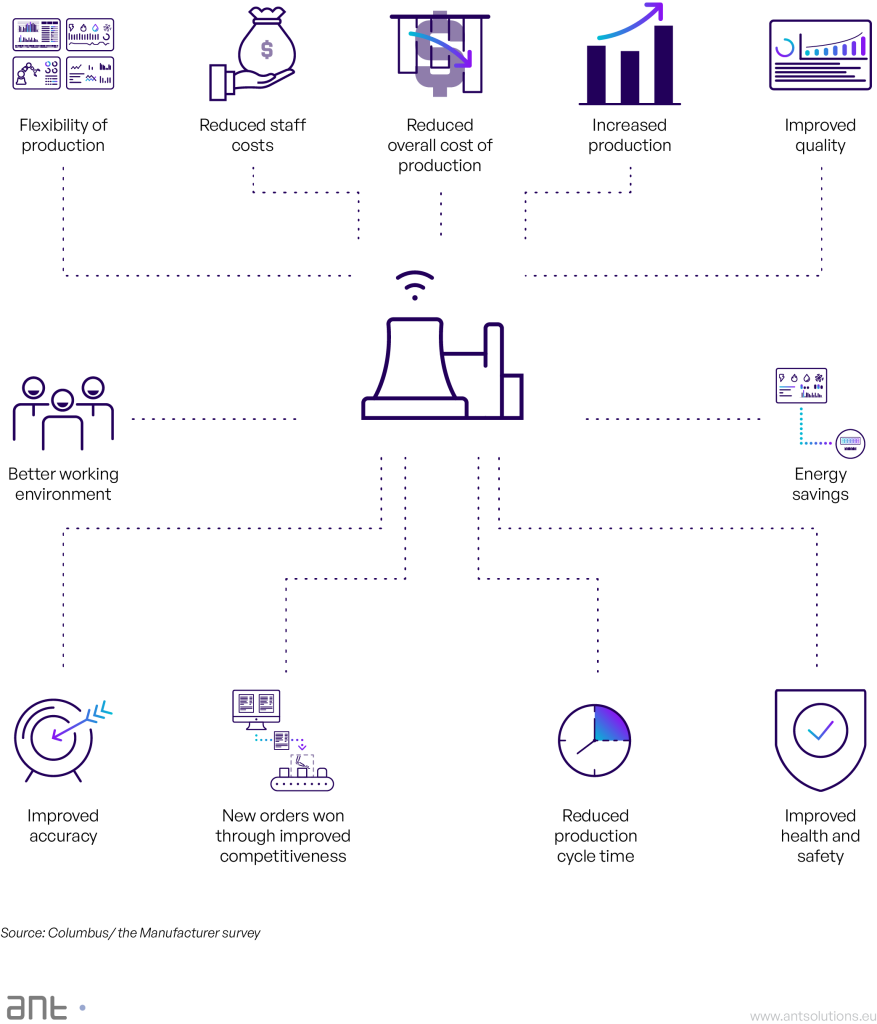
Overcoming Challenges in Smart Manufacturing
Despite its myriad advantages, the shift towards smart manufacturing is not without its challenges. Manufacturing companies often grapple with the integration of new systems into established workflows and the training of employees to adapt to new technologies. This section will offer strategies to navigate these obstacles, ensuring a smooth transition to more efficient and intelligent manufacturing systems.
Integration of new systems into established workflows
Integrating new smart manufacturing technologies into existing workflows can be a complex and challenging task. It is important to carefully plan and manage this process to minimize disruption and ensure a smooth transition.
Here are some strategies for integrating new smart manufacturing technologies into established workflows:
-
- Start small and scale up gradually. Don’t try to implement too many new technologies at once. Start with a few key areas and gradually scale up as you gain experience and expertise.
-
- Involve stakeholders early and often. Get input from all stakeholders, including employees, managers, and customers, throughout the integration process. This will help to identify potential challenges and ensure that the new technologies are meeting the needs of all users.
-
- Provide training and support to employees. It is important to train employees on how to use the new technologies. This will help them to adapt to the changes and ensure that they are able to use the new technologies effectively.
-
- Use a phased approach. Implement the new technologies in phases, with each phase building on the previous one. This will help to mitigate disruption and make it easier to troubleshoot any problems that arise.
The Future of Manufacturing
As we look towards the future, it is clear that emerging technologies will continue to shape the landscape of manufacturing. Augmented reality for training and machine maintenance, 3D printing for on-demand production, and predictive maintenance for uninterrupted operations are just the tip of the iceberg. The potential for further advancements in AI and machine learning promises to make smart manufacturing not just a trend, but a staple of resilient and adaptive manufacturing industries worldwide.
Wniosek
Smart manufacturing is not just an upgrade; it’s a revolution that redefines the manufacturing process from the ground up. For companies poised to adopt smart manufacturing technologies, the promise is a future of unmatched efficiency, quality, and innovation. As we stand on the cusp of this new era, the manufacturing industry must continue to embrace change, driving forward with the same innovative spirit that sparked the very first industrial revolution.
Getting Started with Smart Manufacturing
For businesses contemplating the smart manufacturing leap, the path involves:
-
- Operational Assessment: Pinpoint areas ripe for efficiency and quality enhancement.
-
- Technology Selection: Align technology choices with specific business needs and budgetary considerations.
-
- Scaled Implementation: Start with manageable segments before expanding.
-
- Employee Buy-In: Cultivate a culture of innovation by training employees on new technologies and their advantages.
Produkty związane z tym artykułem

System MES - system realizacji produkcji - ANT Solutions
System MES - Manufacturing Execution System 0 % wydłużenie czasu pracy 0 % redukcja ilości defektów 0 % redukcja zużycia materiałów 0 % czas przezbrojenia

Monitorowanie wydajności OEE
Monitorowanie wydajności (OEE) Podłącz i zbieraj dane z maszyn. Zaplanuj demonstrację. Kluczowe korzyści Wzrost OEE ✔️ krótsze przestoje ✔️ szybsza produkcja

System zarządzania operacjami produkcyjnymi (MOM)
Manufacturing Operations Management System (MOM) Najbardziej kompletne rozwiązanie produkcyjne z pełnym wsparciem dla zarządzania operacjami i łącznikiem pomiędzy automatyką przemysłową a operacjami biznesowymi.