It’s no secret that every step of the pharmaceutical manufacturing process must be documented. However, managing paper documentation can be extremely time-consuming for pharmaceutical manufacturers, and human error can be relatively common.
For this reason, pharmaceutical companies decided to implement what is known as Electronic Batch Record (EBR) in order to both streamline workflow and minimize the possibility of errors creeping in. This article shows how the ANT’s system enables document creation from bulk to packaging processes in the pharmaceutical sector.
Worum geht es beim EBR?
The company from the pharmaceutical industry, who decides to implement new solutions in production, care not only about the digitalisation of forms. EBR solution is also intended to maximize the time required to fill in form fields and lead to automatic form filling by collecting data directly from the machines. Data on the forms may include: product weighing, mixing, granulation, tableting, coating, packaging and quality control. Collecting data directly from equipment such as scales, pH and conductivity meters is usually also a requirement. Additionally, the company wants to avoid errors and track deviations from the norm that happen in the production process.
The implementation of the ANT system brings not only efficient digitisation of documentation. Operators are guided through the production process, including changeovers, quality, logistics and, of course, maintenance processes. The system is compliant with GMP.
Dadurch wurde die Erstellung oder Änderung von Formularen erheblich erleichtert. Dies erfordert jedoch nach wie vor autorisiertes Personal - nur Personen mit dem richtigen Zugang können Änderungen an den Formularen vornehmen. All dies dient dazu, Fehler oder eine unsachgemäße Bearbeitung zu verhindern.
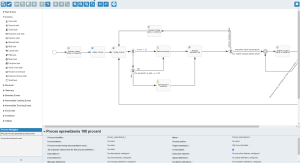
Was bietet die ANT-Lösung für die Pharmaindustrie?
ANT offers a complete system including machine data acquisition, hardware, ERP integration and infrastructure. This system also includes MBR template creation. With Master Batch Record (MBR), clients are able to create templates of the MBR by setting all activities in the system in the right sequence and with responsibility for each role. Each activity can be configured with reporting data types like numbers, text, data read from automation, etc. Those values can then be validated against quality limits set in the system.
A few examples of fields in forms that have been implemented include whether an action has been performed or not. Also, among the changes are a production value field and information about when a specific task was started or stopped, along with a calculation of the time spent on it. Among the implementations, there is also an electronic signature placed on the form and notes or remarks made by the responsible person.
The ANT system also enables automatic collection of process parameter data from production stages. Among these can be highlighted:
Weighing – Mettler-Toledo – Weigh Data and Gareco native protocol
Mixing – Siemens TCP
Granulator – Siemens TCP
Tableting – IMA Kilian – B&R OPC UA
Coating – Glatt – Siemens TCP
Blister packaging line – IMA, which includes: Blister Machine – OPC, Serializer – Digital I/O, Case Packer – Ethernet TCP.
By implementing the solution, every work center is equipped with an operator panel, different models on the white zone, different on grey due to requirements. Some of the actions performed on the operator panel include selecting production order, confirming of done/not done actions, electronic signature, step-by-step instructions, displaying documentation, production progress monitoring, traceability and OEE analysis.
Integration with SAP can be done by WEB services. Additional description of the production process (changeovers matrix, quality control limits, etc.) can be done in the ANT Master Data module.
Wie sieht der papierlose Prozess in der Pharmaindustrie aus?
Paperless process takes into account digitally guiding the operator through specific parts of production, starting with the activity display – the to-do list for production. It also includes changeover information with dedicated documentation for each production step (image, document, video). All paper documents from production are digitized by using ANT Factory Forms.
Thanks to ANT Factory Forms, all sheets, tables and reports are being automatically fielded with the data gathered on current shifts. System monitors and notifies operator in the right moment when the task must be completed. Any changes and deviations are monitored with audit trail.
With validation and traceability of materials, mobile barcode scanners are implemented. The weighing and packaging processes require scanning and confirmation that the material can be used in current production order, thus building traceability and current material stock on WIP. The system supports boxes or containers labels printing and traceability.
When testing samples, the system itself, automatically notifies the operator when a new sample needs to be created. It also notifies the operator to prepare a printout of a new label, prepared by ANT. This label is later scanned by the laboratory, which performs the operations in the plant. The ANT system reads the values from the test equipment and automatically compares the results with the set quality tolerances. The system decides whether the sample is correct or incorrect and sends the information back to the operator panel.
Each batch must go through the approval path in the ANT system to be released. This ties into the workflow factor. Each step must be signed with an electronic signature by the people who notify specific roles in the company. Notifications are sent if the current step in the workflow is assigned to a specific role. People with the right permissions can see where the batch release process has stopped and monitor KPIs for the time taken to complete each step.
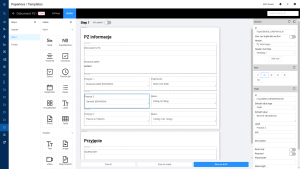
Digitale Aktenverwaltung mit EBR
In summary, all of the factors described above, make EBR work. This enables digital documentation management for the entire production process. The system ensures that the steps are fully populated with all required data. The result of EBR creation is a PDF file with completed reports and signatures.
Welche Vorteile ergeben sich daraus für das Pharmageschäft?
For starters, the system enables a 35% reduction in batch release time thanks to workflow and automated data gathering. There are also 15% less errors and waste produced thanks to material validation, periodical quality checks and step-by-step digital instruction. It also provides a 7% increase in OTIF.
The implementation of EBR also ensures faster communication between company departments, impacts the elimination of paper from the production process, and provides the monitoring of current batch releases statuses round the clock.
ANT has the solutions your pharmaceutical business needs to make workflows more efficient and environmentally friendly. For more personalized advice, feel free to contact a member of the team.
Produkte in diesem Artikel

Papierlose
Fertigung
Paperless Manufacturing Streamline your manufacturing with ANT PAPERLESS. Digitize forms, improve communication, and access data securely from anywhere, creating a more efficient and sustainable operation.

Software für elektronische Chargenprotokolle (EBR)
Electronic Batch Records (EBR) Software: A Digital Solution for Streamlined Batch Management Electronic Batch Records (EBR) software replaces traditional paper-based batch records, offering digital guidance