A smart factory is a manufacturing facility that uses advanced technologies to collect and analyse data, automate processes, and make decisions in real time. Smart factories are more efficient, productive, and sustainable than traditional factories. They can produce higher quality products at lower costs, and they can respond to changes in demand more quickly.
Smart Factory is a basic term of Industry 4.0 (Fourth Industrial Revolution) concept and ultimate goral of digital transformation process.
What is the difference between a traditional factory and a Smart Factory?
In a standard factory, operations are largely manual and paper-based. Data is collected and from collecting data is entered into systems manually, and communication is often slow and inefficient. As a result, standard factories can be prone to errors, delays, and waste.
Smart factories, on the other hand, use sensors and other devices to collect data from machines and processes in real time. This data is then analysed using artificial intelligence and machine learning to identify trends, patterns, and potential problems. This information is then used to optimise operations, improve quality, and make better decisions faster.
Featureย | Standard Factoryย | Smart Factoryย |
Data collectionย | Manualย | Real-timeย |
Communicationย | Slow and inefficientย | Efficient and fastย |
Reportingย | Duplicateย | Single source of truthย |
Indicatorsย | Inaccurateย | Accurateย |
Documentationย | Paper-basedย | Digitalย |
Errorsย | Highย | Lowย |
Response to errorsย | Delayedย | Instantย |
Downtimeย | Commonย | Rareย |
Control over machineryย | Limitedย | Comprehensiveย |
Inventory managementย | Suboptimalย | Efficientย |
Utility consumptionย | Uncontrolledย | Controlledย |
Greenhouse gas emissionsย | Unaccounted forย | Accounted forย |
Readiness for changeย | Lowย | Highย |
Sustainabilityย | Lowย | Highย |
In the smart factory, sensors and other devices are collecting data from machines and processes in real time. This data is then analyzed using artificial intelligence and machine learning to identify trends, patterns, and potential problems. This information is then used to optimize operations, improve quality, and make better decisions faster.
The Introduction of Industrial Automation
The introduction of industrial automation has a long and rich history, dating back to the early 19th century. The first industrial automation devices were simple machines that were used to automate repetitive tasks, such as weaving and spinning. As technology advanced, more sophisticated automation devices were developed, such as the programmable logic controller (PLC) in the 1970s.
PLCs revolutionized industrial automation by making it possible to create complex and flexible automation systems. PLCs can be used to control a wide range of machines and equipment, and they can be programmed to perform a variety of tasks. This flexibility has made PLCs the most widely used automation devices in the world.
The introduction of industrial automation has had a profound impact on the manufacturing industry. Automation has led to significant increases in efficiency and productivity, and it has also helped to improve the quality of manufactured products. In addition, automation has created new jobs in the fields of engineering, maintenance, and programming.
Today, industrial automation is used in a wide range of industries, including manufacturing, automotive, food and beverage, aerospace, and healthcare. Automation is helping businesses to improve their efficiency, productivity, quality, supply chain management and competitiveness.
What Technologies are used in a Smart Factory today?
Smart factories use a variety of technologies to improve efficiency, productivity, and quality. Some of the most common technologies include:
Internet of Things (IoT): IoT devices collect data from machines, sensors, and other equipment throughout the factory. This data can be used to track production progress, identify potential problems, and make better decisions.
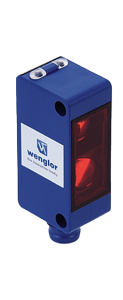
Artificial intelligence (AI): AI is used to analyse data from IoT devices and other sources to identify patterns and trends. This information can be used to predict problems, optimize production, and make better decisions.
Robotics and automation: Robots and automation are used to perform tasks that are repetitive, dangerous, or difficult for humans to do. This can free up workers for more complex work and improve the overall efficiency of the factory.
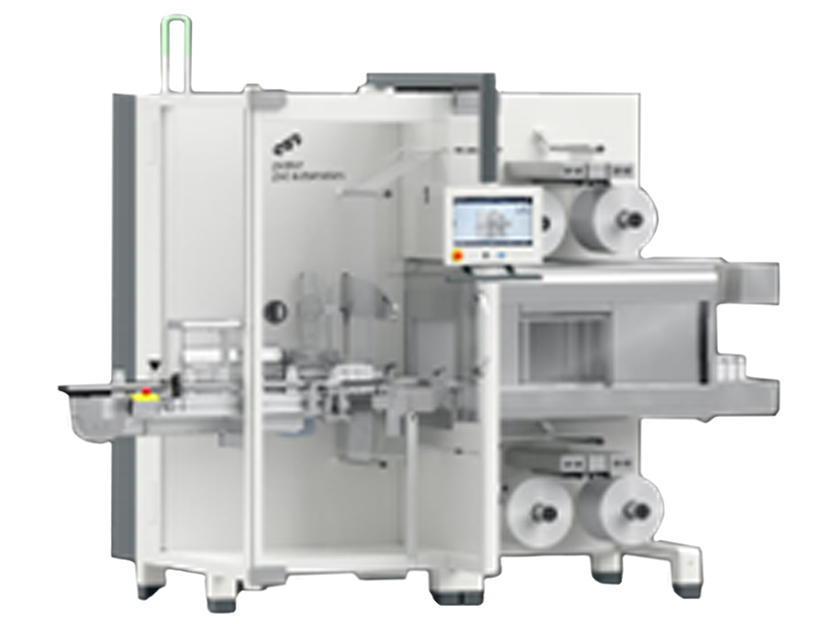
Big data analytics: Big data analytics is used to process and analyse large amounts of data from IoT devices and other sources. This information can be used to identify trends, patterns, and insights that would be difficult to find manually.
Digital twins: Digital twins are virtual representations of the physical factory. They can be used to simulate production processes and identify potential problems before they occur.
Additive manufacturing (3D printing): 3D printing is used to create prototypes and custom parts. This can reduce the time and cost of product development and manufacturing.
Edge computing: Edge computing is a decentralised approach to computing that brings processing power and storage closer to the source of data. This can improve performance and reduce latency in smart factories.
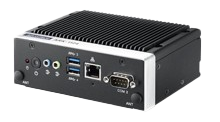
Cloud computing: Cloud computing provides a platform for storing and processing data from IoT devices and other sources. It also provides access to software applications that can be used to analyse data and manage production.
Manufacturing software: IT solutions provide a backbone of modern digital factory. They allow to seamlessly transfer data from physical to digital world, tracking progress and ensure end-to-end traceability.
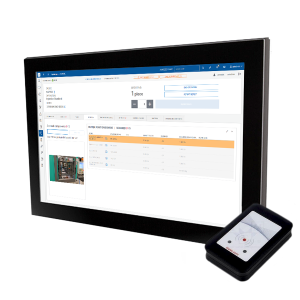
Augmented reality (AR): AR is used to provide workers with real-time information about the machines and products they are working on. This can improve efficiency and quality.
Factories face numerous challenges both at the local and global levels
Local challenges
Global challenges
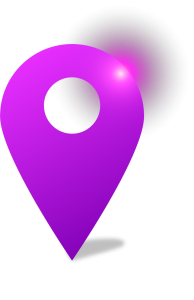
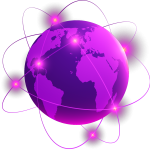
-
- Low Overall Equipment Efficiency (OEE)
-
- Inadequate process control
-
- Inefficient human-machine and
machine-machine communication
- Inefficient human-machine and
-
- Inefficient utilization of resources
-
- Unidentified downtime and failures
-
- Decreased machine availability
-
- Dispersed data and lack of data-driven
problem analysis
- Dispersed data and lack of data-driven
-
- Lack of visibility on the shop floor
-
- Lack of integration between systems
-
- Lack of machine information
-
- Implementation of strategies outlined
by the EU in documents such as:
โฆ Climate-neutral economy by 2050
โฆ European Green Deal
โฆ Need to eliminate the negative
impact of the industry on the climate
โฆ Taking actions to reduce greenhouse
gas emissions
- Implementation of strategies outlined
-
- Enabling users to access and utilize data
from devices and IoT based on the new
Data Act policy
- Enabling users to access and utilize data
-
- Rising energy and material costs
-
- Workforce issues
Do you recognise any of these problems in your factory?
If so, your factory is not smart.
A smart factory is a manufacturing facility that uses digital technologies to improve efficiency, productivity, and quality of manufacturing processes. Smart factories use data and analytics to make better decisions, automate tasks, and predict problems.
The list of problems in the image above are all common challenges that manufacturing companies face. Smart factory technologies can help to solve these problems and improve the overall performance of the factory.
For example, smart factory technologies can be used to:
-
- Reduce downtime by predicting and preventing machine failures.
-
- Improve quality by identifying and correcting defects in real time.
-
- Increase visibility into production progress so that managers can make informed decisions.
-
- Automate manual tasks to free up workers for more complex work.
-
- Improve traceability of products and materials so that companies can meet customer requirements and regulatory compliance.
If you are facing any of the problems on the list above, it is time to consider investing in smart manufacturing practices and factory technologies. Smart factories can help you to improve your bottom line and stay competitive in today’s global marketplace.
How can a smart factory improve efficiency and productivity?
The transition from traditional factories to Smart Factories is a leap not just in terms of technology, but also in the potential advantages it can offer to manufacturers, employees, supply chains, and even the end consumers. Here’s an in-depth look at the benefits of a Smart Factory:
- Enhanced Productivity:
- Smart factories optimize processes, minimize downtime, and automate routine tasks, leading to a surge in production levels.
- Advanced robotics and AI-driven systems can operate 24/7 without fatigue, ensuring uninterrupted production cycles.
- Efficient Resource Utilization:
- Advanced analytics allow for a more accurate prediction of material requirements, reducing waste.
- Energy consumption is optimized through smart grids and sensors, leading to sustainable operations and cost savings.
- Increased Flexibility:
- Smart factories can easily adapt to changes in product design or production volume.
- They can seamlessly shift between different tasks, allowing for a more diverse product range without reconfiguring the entire setup.
- High-Quality Production:
- Consistent monitoring and real-time feedback mechanisms ensure that products meet strict quality standards.
- Defective products are quickly identified and isolated, reducing recalls and enhancing brand reputation.
- Predictive Maintenance:
- Instead of waiting for a machine to break down, data analytics predict when maintenance is needed, reducing unexpected downtimes.
- This proactive approach extends the lifespan of machinery and reduces long-term maintenance costs.
- Cost Savings:
- With increased efficiency and reduced waste, smart factories often lead to significant financial savings in the long run.
- Inventory costs are minimized with just-in-time manufacturing and optimized supply chain dynamics.
- Improved Worker Safety:
- Automation reduces the need for human intervention in potentially hazardous tasks.
- Real-time monitoring can detect unsafe conditions, triggering immediate preventive actions.
- Real-time Decision Making:
- Managers and stakeholders can make informed decisions based on real-time data from the factory floor.
- Instant access to this data allows for quicker reactions to market changes, supply chain disruptions, or production issues.
- Customization Capabilities:
- Smart factories can efficiently handle customized orders, allowing businesses to cater to specific customer needs without compromising on production speed.
- This enhances customer satisfaction and opens new market segments.
- Supply Chain Optimization:
- Integrated systems provide insights into every step of the supply chain, ensuring timely raw material delivery and finished product distribution.
- Delays and inefficiencies are minimized, leading to a smoother and more reliable production process.
- Environmental Benefits:
- Reduced waste, optimized energy consumption, and sustainable practices mean smart factories have a lower carbon footprint.
- They align more with global sustainability goals, enhancing the brand image and fulfilling corporate social responsibilities.
How does a smart factory affect people’s jobs?
The impact of smart factories on people’s jobs is complex and multifaceted. On the one hand, smart factories can lead to job losses, as some tasks that are currently performed by humans can be automated. On the other hand, smart factories can also create new jobs, as new skills are required to design, implement, and operate smart factory solutions and technologies.
Overall, the impact of smart factories on people’s jobs is likely to be positive in the long term. Smart factories can make the entire production process of manufacturing more efficient and productive, which can lead to economic growth and job creation. However, there is a risk that some workers will be displaced in the short term as smart factory technologies are implemented.
Here are some specific ways that smart factories are affecting people’s jobs:
-
- Automation: Smart factories are automating many tasks that are currently performed by humans, such as assembly line work, quality control, and material handling. This can lead to job losses, but it can also free up workers for more complex and skilled tasks.
-
- New skills: Smart factories require new skills to design, implement, and operate smart factory technologies. This is creating new jobs for engineers, data scientists, and other skilled workers.
-
- Upskilling and reskilling: Many workers who are displaced by smart factory technologies will need to be upskilled or reskilled to learn new skills for the smart factory environment. This can be a challenge, but it is important to ensure that all workers have the opportunity to benefit from the transition to smart manufacturing.
Governments and businesses have a role to play in helping workers to transition to the smart factory economy. Governments can provide support for upskilling and reskilling programs. Businesses can invest in training their workers on new skills and creating new jobs for workers who are displaced by automation.
How can a smart factory improve efficiency and productivity?
Smart factories can improve efficiency and productivity in a number of ways:
-
- Real-time data collection and analysis: Smart factory technologies collect data from machines, sensors, and other equipment in real time. This data can be used to track production progress, identify potential problems, and make better decisions. For example, machine learning algorithms can be used to predict machine failures before they occur, which can help to reduce downtime and improve efficiency.
-
- Automation of manual tasks: Smart factories can automate many manual tasks that are currently performed by humans. This can free up workers for more complex and skilled tasks, which can lead to increased productivity. For example, robots can be used to perform assembly line work, freeing up workers to troubleshoot problems and improve quality.
-
- Improved visibility and traceability: Smart factory technologies provide real-time visibility into production progress and traceability of products and materials. This can help to identify and address bottlenecks, reduce waste, and improve quality. For example, RFID tags can be used to track the movement of products through the production process, which can help to identify and address delays.
-
- Collaboration between humans and machines: Smart factory technologies can be used to create a more collaborative environment between humans and machines. For example, augmented reality (AR) can be used to provide workers with real-time information about the machines and products they are working on. This can help workers to perform their tasks more efficiently and accurately.
What benefits do companies experience/expect from factory digitalisation?
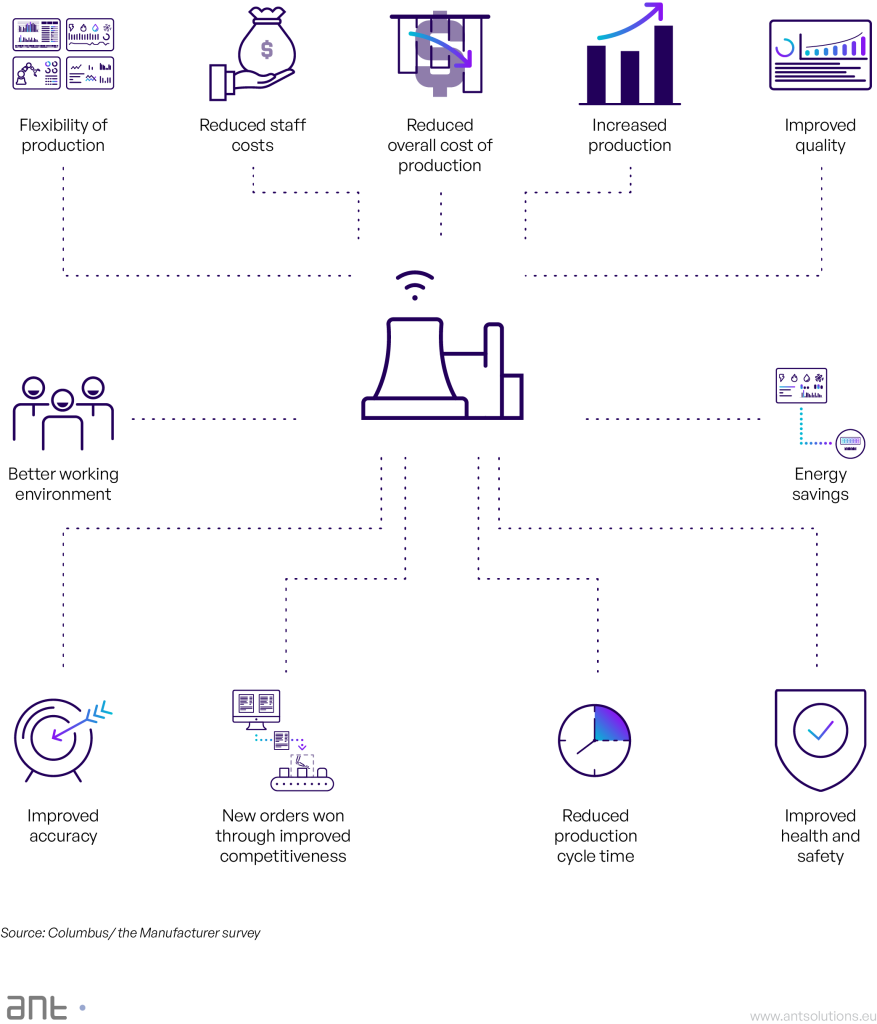
What are potential risks and challenges in implementing a Smart Factory?
-
- Cost: Smart factory technologies can be expensive to implement and maintain. This can be a barrier for small and medium-sized businesses.
-
- Complexity: Smart factories are complex systems that require careful planning and implementation. There is a risk of things going wrong, which can be costly and disruptive.
-
- Security: Smart factories are connected to the internet, which makes them vulnerable to cyberattacks. It is important to implement strong security measures to protect smart factory systems and data.
-
- Change management: Implementing a smart factory can require significant changes to existing processes and workflows. It is important to manage this change carefully to ensure that employees are on board and that the transition is smooth.
-
- Skills gap: There is a shortage of skilled workers who have the skills and knowledge to design, implement, and operate smart factory technologies. This can make it difficult to find the right talent to implement a smart factory.
Concerns Surrounding Factory Connectivity Implementation and Continuation
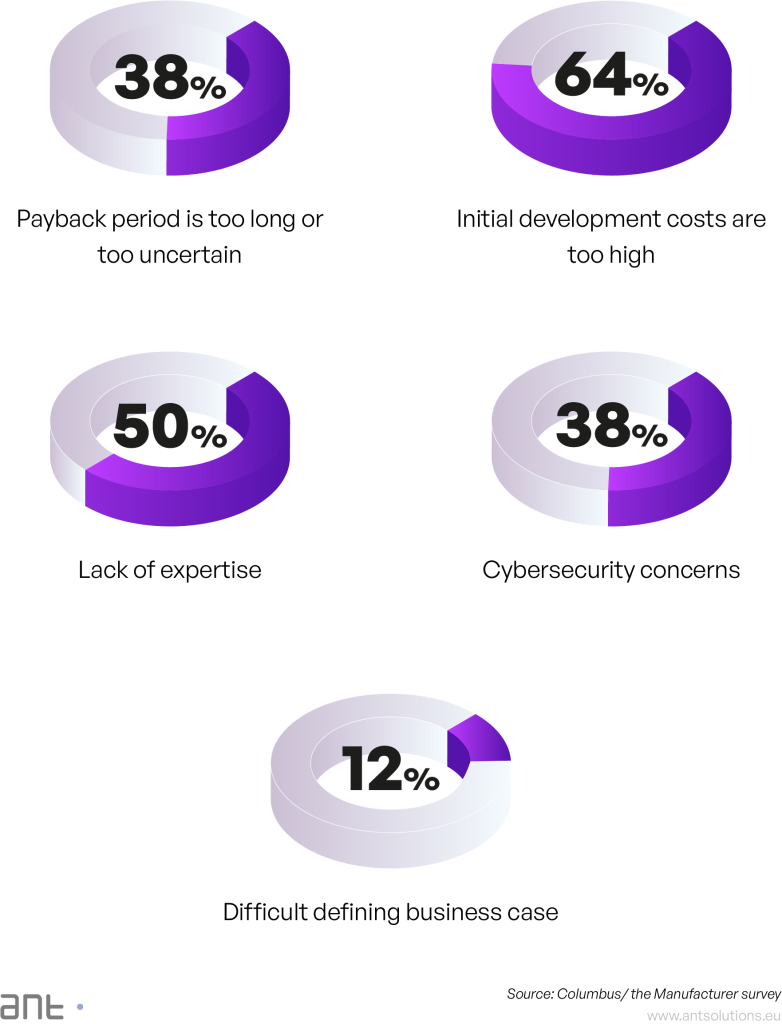
Measuring Success & ROI of Smart Factory
Defining key performance indicators (KPIs) to measure the impact of smart factory implementation
In the realm of smart factory implementation and the integration of modern IT systems, measuring
success and return on investment (ROI) plays a pivotal role in determining the effectiveness and
value of these initiatives. Defining key performance indicators (KPIs) provides organisations
with tangible metrics to assess the impact of their smart factory endeavours. Some examples of
KPIs in this context include production throughput, machine downtime, quality metrics, and energy
consumption. By monitoring production throughput, companies can evaluate the efficiency and
speed at which products are manufactured, ensuring optimal utilisation of resources and
minimising bottlenecks. Tracking machine downtime helps identify opportunities for
maintenance optimisation, reducing costly production interruptions. Quality metrics enable
organisations to measure product defects, rework, and customer satisfaction, thereby ensuring
the delivery of high-quality products. Lastly, monitoring energy consumption helps identify
energy-saving opportunities, leading to cost reduction and environmental sustainability. By
defining and analysing these KPIs, businesses can gain valuable insights into the success and ROI
of their smart factory implementation, driving continuous improvement and growth.
It is important to note that the specific KPIs and metrics used to measure the success and ROI
of smart factory implementation can vary depending on the unique characteristics of each
factory and the specific IT systems being adopted. Factors such as the industry, product type,
production processes, and customer requirements all play a crucial role in determining the relevant
KPIs for a given scenario. For example, a factory focused on lean manufacturing might prioritise
metrics such as lead time reduction, inventory turnover, and waste reduction. On the other hand, a
factory with a strong emphasis on customer responsiveness might prioritise KPIs related to
on-time delivery, order fulfilment accuracy, and customer satisfaction ratings. By tailoring the
selection of KPIs to align with the specific objectives and requirements of the factory, organisations
can ensure a comprehensive evaluation of the impact and success of their smart factory
implementation.
Download our Smart Factory Report with detailed case study including ROI
In conclusion
A smart factory represents the technological and digital evolution of traditional manufacturing setups. By leveraging advanced technologies such as AI, IoT, data analytics, and automation, smart factories offer a range of benefits:
-
- Enhanced Productivity: These factories optimize operations and can run 24/7 due to AI-driven systems and robotics, minimizing human-induced downtimes.
-
- Efficient Resource and Energy Use: Predictive analytics reduce waste, and sensors optimize energy consumption, leading to sustainability and cost savings.
-
- Flexibility and Customization: Smart factories can swiftly adapt to design changes or varying production volumes, and they can efficiently handle customized orders, allowing businesses to address specific customer demands without sacrificing production pace.
-
- Quality and Predictive Maintenance: Continuous monitoring ensures high-quality production, quickly identifying defects. Predictive maintenance reduces unexpected machine downtimes, leading to extended machine lifespan and cost savings.
-
- Improved Safety and Real-time Decision Making: Automation and real-time monitoring enhance worker safety and facilitate immediate, data-driven decision-making.
-
- Supply Chain Optimization and Environmental Benefits: Integrated systems streamline the entire supply chain and reduce the environmental impact, aligning with global sustainability goals.
However, the transition also poses challenges such as potential job displacement due to automation. While some roles may become obsolete, new opportunities for skilled workers, like data scientists and engineers, will emerge. The implementation of smart factories requires significant investment, and companies face potential risks like cybersecurity threats, integration issues, and the need for employee upskilling. Yet, by tracking key performance indicators, businesses can measure and optimize the return on investment from their digital transformation initiatives.
Products related to this articleโ

OEE Performance monitoring
Performance Monitoring (OEE) Connect and gather data from your machines. Schedule a Demo They Trusted Us: Key Benefits OEEincrease โ๏ธ shorter downtimes โ๏ธ faster production

Manufacturing Operations Management System (MOM)
Manufacturing Operations Management System (MOM) The most complete manufacturing solution with full support for operations management and a link between industrial automation and business operations

MES System – Manufacturing Execution System – ANT Solutions
System MES – Manufacturing Execution System 0 % operating time increase 0 % defects quantity reduction 0 % material consumption reduction 0 % changeovers time